Based on a white paper by Neil Faulkner and Jeff Gust, Fluke Calibration
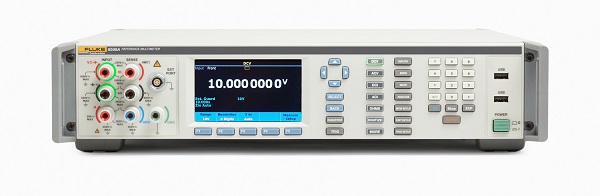
Abstract
Historically, analog null meters, also called analog null detectors, have been used to determine zero voltage conditions in metrological applications. When digital multimeters (DMMs) became available with sensitivity comparable to null meters, they were adopted quickly, and analog null meters were set aside. However, depending on the circuit and the DMM, significant measurement errors can be introduced. This paper discusses in detail one particular model of precision DMM, when used as a null meter, and provides measurement configuration details to minimize errors so that the DMM can out-perform analog null meters.
Introduction
Since the 1960’s commercial voltage and ratio calibrators have been available to calibrate dc voltage, from very low levels on the order of millivolts, to relatively high values up to 1 kilovolt. A critical component of these systems was the analog high impedance voltmeter/null meter. These instruments were generally designed for extremely high input impedance (10 to 100 MΩ), excellent sensitivity (0.1 μv per division) and high isolation (on the order of 1012 Ω).
To perform precision dc voltage measurements, an analog null meter such as the Fluke 845AB was used with precision voltage dividers such as the Fluke Calibration 720A Kelvin Varley Divider, or more recently the Fluke Calibration 752A Reference Divider and a zener reference standard. When performing precision voltage measurements with a 752A, a null meter is also required to align (also referred to as self-calibrate) the divider ratio of 10:1 to 0.2 parts in 106 and the 100:1 divider ratio to 0.5 parts in 106 of its ratio quantity.
To obtain valid results, several issues must be considered in the setup and alignment of the 752A. For example, during alignment, the voltage measured by the null meter is sourced through an equivalent resistance as high as several hundred k ohms. Any source noise or current emanating from the null meter can introduce an additional voltage into the divider circuit, causing errors in aligning the ratio quantity. Once the 752A has been aligned, it is used with a zener reference standard such as the Fluke Calibration 732C. Together, the 732C, 752A and null meter are used to calibrate output voltage quantities such as those on a voltage calibrator, or to perform a short term characterization of a voltage source for subsequent calibrations of voltage measuring devices.
By the 1970’s, Fluke and other manufacturers began producing precision digital multimeters, and by the 1990’s several models were available with resolutions/sensitivities that were comparable to the 845AB; in fact, Fluke no longer manufactures the 845 series because of the availability and advantages of using DMMs, such as automated control and capture of data. However, not every DMM can be used as a direct substitute for the 845 series null meter. The DMM can introduce errors in the process of aligning the divider, and its use is associated with errors due to input impedance, isolation, source noise and source current. Even in such cases, a DMM can be used to get good results, with proper configuration and procedures that greatly reduce these errors.
Discussion
Fluke has developed a recommended protocol for the configuration of the 8588A and similar DMMs for use in aligning the 752A, and for using it as a null meter in conjunction with the 752A. Failure to utilize this protocol may result in errant measurements.
The 752A is a precision dc voltage divider with 10:1 and 100:1 ratios. It is designed to be aligned using a stable 20 volt low noise source (generally a calibrator like a Fluke Calibration 5730A Multifunction Calibrator) and a null meter. To align the 752A, it is set to the calibration mode, which configures the divider resistors into a Wheatstone Bridge configuration (see Figure 2). Current emanating from the 8588A through the resistors in the bridge can cause a significant error in the alignment of the voltage divider. There are two sources of this current. A simplified diagram of the bridge, for the purpose of showing the path and effect of these currents, is shown in Figure 1.
Figure 1. Fluke Calibration 8588A with equivalent resistance circuit of the 752A Reference Divider in the calibration mode
The first source of current from the 8588A is a dc current flowing between the meter HI and LO input terminals, due to the input bias current from the input operational amplifiers. The specification for this current is 20 pA, but it is almost always less than 5 pA. This current passing through the bridge resistance causes an error of 0.4 μV, which equals approximately 0.1 part in 106 for the 10:1 ratio and 1.3 μV for the 100:1 ratio, which then equals approximately 0.25 parts in 106. This is a significant offset that must be accounted for. The second source of current is generally referred to as pumpout current, which appears in the form of current spikes. In the case of the 8588A, the spikes are in sync with the ac line frequency. This current seeks a path to ground and can cause an offset in the meter reading as it follows through the 60 kOhms equivalent resistance to ground, as shown in Figure 1.
Tests performed on a number of meters showed that this offset was generally insignificant, but it still should be considered. Offsets may also occur from meter zero drift and as a result of its connection to the 752A. Accounting for these offsets can be accomplished as follows. Connect the meter HI and LO to the 752A detector terminals. This should be accomplished with low thermal leads. Set the meter to the 100 mV range and 7 digit resolution. Connect the 5730A HI and LO to the 752A INPUT and have the 5730A set to Internal Guard. Connect the 5730A Guard and Ground together and to the 752A Guard and Ground. Set the 752A to the CALIBRATE mode 10:1+ and the 5730A to 0 Volts and OPERATE. It is very important that the 5730A be in OPERATE to provide a path for the pumpout current to Ground. After the reading on the meter settles, use the “ZERO”, “F1 – Zero Range” button sequence to zero the meter. Zeroing the meter accounts for the offsets created by currents emanating from the 8588A for the 10:1 calibration, and it must be repeated for the 100:1 calibration as the offset will be different. A detailed description of the entire self-calibration procedure with schematics can be obtained from the paper authors.
Figure 2. Schematic of the 10:1 divider circuit of the Fluke Calibration 752A Reference Divider in the calibration mode
The 752A was designed to accommodate the use of a 10 V zener reference standard and a null meter to calibrate a voltage source from 100 mV to 1000 V. Here again the Fluke Calibration 8588A can be used as the null meter. The output resistance of the divider is 36 k Ohms for the 10:1 ratio and 40 k Ohms for the 100:1 ratio. The 8588A input bias current can generate an offset that is significant for a 100 mV calibration. The error due to the pumpout current is insignificant if the output resistance of the source under test is low, as is generally the case. The meter offset and zero drift must also be accounted for. To correct for these offsets, connect the meter as previously described. Connect a low thermal EMF short to the 752A INPUT and REFERENCE STANDARD terminals. Set the 752A CALIBRATE switch to OPERATE and the MODE switch to 0.1 V. This sets the 752A to the 100:1 ratio. When the reading settles, perform the meter zero as per the operational instructions. This corrects for offsets on the 100:1 ratio. When the 752A is in the 10:1 ratio, it is not necessary to zero the meter again as the uncorrected offset will be insignificant at 1 V and above.
Conclusion
The Fluke Calibration 8588A Reference Multimeter can be a suitable replacement for analog null meters, if appropriate corrections are made for current emanating from the meter input terminals. Before any other digital multimeter is used as a null meter, the input bias current and other current sources must be considered to determine the significance of error generation to the circuit.